The system is very economical to operate, typically requiring only one operator for production and the electrical power necessary to drive but two or three 1 horsepower motors. The only additional operating costs are that of the liquid nitrogen, essential for the freezing process, which is very economical and cost efficient.
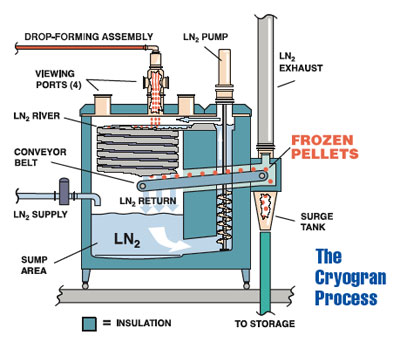
The strength of the patented Cryogran technology is in its ease of operation. Liquid nitrogen is supplied to the Cryogran either from a permanent outside storage facility or from a temporary source such as portable dewars which are available in a host of sizes under 500 litres.
All aspects of the Cryogran operation are controlled by the Cryogran central control panel utilizing a PLC logic controller. Liquid nitrogen flow to the Cryogran is controlled via a specialized pressure-level sensing system operating in conjunction with a solenoid valve. The equipment calls for liquid nitrogen when needed and shuts of the supply when normal operating parameters are achieved. A constant digital readout of these levels is provided.
The liquid nitrogen pump then transports the liquid nitrogen from the sump area to the beginning of the sluiceway located at the top of the equipment. This creates a flowing “river” of liquid nitrogen that descends in a spiral or linear fashion down the sluiceway trays. Product droplets are created and deposited via a specialized fillinghead assembly that creates and strategically introduces them into the moving cryogenic flow at the top of the sluiceway. As the droplets enter the river of cryogenic fluid they instantly form a hard outer shell, ensuring their spherical shape. The river then carries the newly introduced droplets downward along its course allowing for the completion of the deep-freezing process. Upon conclusion of the pellets’ journey at the bottom of the sluiceway, they are exited from the equipment on a stainless steel wire mesh conveyor belt. The liquid nitrogen at that point passes through the belt back into the sump area for recirculation within the system.